Acid gas scrubbers are commonly used for the removal of acid gases, such as sulfur dioxide, hydrochloric acid, chlorine, hydrofluoric acid, and nitrogen dioxide. These scrubbers typically use a basic reagent; often sodium hydroxide, soda ash, or lime to keep the scrubber liquor at neutral to high pH.
Operation at a high pH can lead to unexpected problems with water chemistry. Calcium carbonate, calcium sulfate, and calcium fluoride all can cause scale within the scrubber. Scale can reduce the effective pipe diameters, coat packing, block nozzles, foul instrumentation. In the worst extremes, calcium scale can shut down the scrubber and in turn shut down the upstream process equipment.
How does one avoid such hazards? In the first of this two part series, I will go through the five steps for determining if calcium scale is a threat to your acid scrubber.
Step 1: Determine the calcium concentration
Calcium primarily infiltrates an acid scrubber through two sources: water makeup and chemical addition. Water makeup is typically from a municipal or well source. The calcium concentration can usually be found in municipal water reports. Well water can be tested cheaply at an outside laboratory for calcium.
Calcium content for sodium hydroxide and soda ash is a bit more difficult to determine, but can be specified in the procurement of the chemicals. Using the chemical consumption rate and the blow down flow rate, the amount of calcium left in the scrubber water can be calculated. Lime actually contains calcium, and should be avoided where calcium scale is possible.
Step 2: Determine the scaling anion concentrations
The three most common calcium scaling anions are carbonate, sulfate, and fluoride. Carbonate primarily enters the system through fresh water, though in acid gases with high carbon dioxide content carbonate can also absorb into the water. Sulfates enter through fresh water, but due to the high solubility of calcium sulfate, rarely cause problems due to makeup water sulfate. Instead, sulfates are a byproduct of the neutralization of SO2. SO2 neutralizes to HSO3 and SO3 in water, and can convert to SO4 depending on the residence time, pH, temperature, and oxygen content of the acid gas.
Step 3: Calculate the buildup of calcium and the scaling anions.
Determining the concentration of ions in the scrubber requires two steps.
1. Sum all of the mass flow rates (mg/min) of the ion into the scrubber water, including makeup water, chemical, and absorption from the gas.
2. Divide the mass flow rates by the blow down flow rate (L/min) to give a concentration (mg/L).
Step 4: Calculate the LSI index
The most common form of calcium scale is calcium carbonate. Calcium carbonate is formed by the interaction of calcium with carbonate alkalinity. Carbonate alkalinity is often present in fresh water; carbon dioxide can also dissolve in water to create carbonates.
The LSI index offers the best method for determining calcium carbonate scaling; Edstrom provides a wonderful explanation at their website.
Step 5: Calculate the sulfate and fluoride solubilities
The final step is to determine the sulfate and fluoride solubilities.
Calcium sulfate is relatively soluble, but calcium sulfate scale can still occur in SO2 scrubbers. Scale forms for calcium sulfate if the solubility product exceeds 4.93x10^-5. The solubility product for calcium sulfate is equal to the concentration of calcium (mol/L) times the concentration of sulfate (mol/L). The calcium concentration can be converted from mg/L to mol/L by dividing by 40,000. The sulfate concentration can be converted from mg/L to mol/L by dividing by 96,000.
Calcium fluoride is the opposite of calcium sulfate; it is extremely insoluble. Scale forms for calcium fluoride if the solubility product exceeds 3.45x10^-11. The solubility product for calcium fluoride is equal to the concentration of calcium (mol/L) times the square of the concentration of fluoride (mol/L). The calcium concentration can be converted from mg/L to mol/L by dividing by 40,000. The fluoride concentration can be converted from mg/L to mol/L by dividing by 96,000.
Click on the icon below to download a white paper about other challenges associated with acid gas scrubbers.
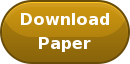