A common wet scrubber air pollution control application is the removal of sulfur dioxide (SO2) and related compounds from combustion processes. This class of compounds is often referred to as SOx. The formation of SOx and SO2 occurs from sulfur bearing fuels or materials oxidizing to SO2 upon combustion. SO2 has negative health effects and can contribute to respiratory illness, especially in children, the elderly, and individuals with pre-existing conditions. In addition to health effects, SO2 contributes to acid rain which can harm plants, trees, rivers, streams, and lakes. SO2 also reacts with other compounds in the atmosphere to form small particles that contribute to particulate matter (PM) pollution and regional haze otherwise known as smog. Regulatory agencies often control SO2 not only to minimize harmful health affects but to reduce regional haze.
Packed bed scrubbers are often considered the best available control technology (BACT) for SO2 removal. Below is a summary of SO2 exhaust streams Envitech has treated using packed bed scrubbers.
- Waste oil refinery waste gas thermal oxidizer and direct fired heater
- Refinery sulfur recovery unit (SRU) thermal oxidizer
- Geothermal power generation regenerative thermal oxidizer
- Secondary lead smelter furnace
- Mineral processing furnace
- Catalyst regeneration kiln
- Ceramic tile kiln
- Hazardous waste combustor
- Medical waste incinerator
- Marine diesel engine
In these applications Envitech has treated SO2 loads as high as 48 tons per day and achieved efficiencies exceeding 99.9% removal. Gas flow rates can vary from < 500 cfm to more than several hundred thousand cfm.
HOW DOES THE TECHNOLOGY WORK?
An example of a large refinery/petrochemical thermal oxidizer SO2 scrubber application illustrates the technology. Below is a summary of design conditions. Liquid discharge limits for chemical oxygen demand (COD) and biochemical oxygen demand (BOD) require oxidation of the blow
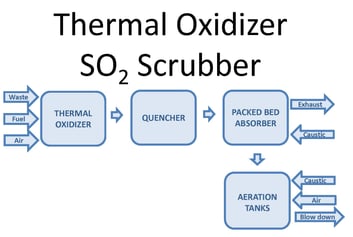
down.
Design Conditions
- Flow rate: 300,000 acfm
- Temperature: 1560oF
- SO2: 300 lb/hr
- Chemical oxygen demand (COD): < 200 mg/l
- Biochemical oxygen demand (BOD: < 50 mg/l
- SO2 removal > 99%
The above figure shows the scrubber equipment arrangement. Waste gas, fuel, and air are fed into the thermal oxidizer. Combustion in the thermal oxidizer generates exhaust gas of 300,000 acfm @ 1,560oF with 300 lb/hr of SO2. The first step of the scrubbing process cools the gas to saturation using adiabatic cooling through evaporation of water. Excess water flows into the packed bed absorber sump.
The next step is SO2 absorption via mass transfer promoted by high efficiency packing media. The gas flows vertically upward, counter-current to downward flowing recirculation water. Neutralization via caustic addition improves the SO2 absorption rate. An entrainment separator at the top of the packed bed absorber removes water droplets in the gas before exiting the system. Water from the absorber sump is recirculated to the quencher and to the top of the packed bed. Make-up water replaces evaporation and blowdown losses.
The SO2 load is low enough that the scrubber absorber sump can serve as an oxidation tank. Air is sparged into the sump to oxidize sulfites (SO-23) to sulfates (SO-24) in order to meet COD and BOD limits. Caustic addition ensures sulfate formation and minimizes sulfur dioxide off-gassing. Larger SO2 loads may require external oxidation tanks.
The adjacent figure shows a typical arrangement to handle 300,000 acfm of gas flow. The system is modularized with 12 feet diameter shop fabricated vessels. Recirculation pump skids and aeration pump skids are pre-assembled in the shop. Instruments are pre-mounted in the piping assembly where possible and pre-wired to a junction box on board the skid. Shop fabrication and assembly minimizes installation time and cost.
Advantages of a packed bed scrubber includes:
- High removal efficiency
- Proven technology
- Low capital cost
- Automatic operation
- High reliability, low maintenance
Click on the link below to download literature about SO2 scrubbing.