Back in July I wrote a blog post for gasification syngas cleaning where I discussed two general approaches, 1) thermal tar destruction, and 2) tar removal scrubbers. Both approaches require particulate removal. This blog post discusses several design considerations related to particulate control for syngas wet scrubber systems, including:
-
Performance
- Capital Cost
- Operating Cost
- Safety
These considerations will be discussed in the context of two wet scrubber approaches for particulate control:
-
- Wet Electrostatic Precipitator
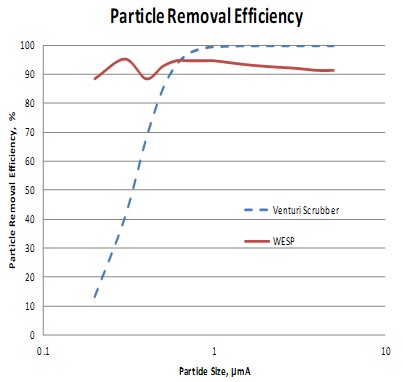
Performance - The distinguishing feature between a Venturi scrubberand a wet electrostatic precipitator (WESP) is the removal efficiency for sub-micron particulate. This is shown in the above figure which compares the particle removal efficiency for a wet electrostatic precipitator (WESP) and a 50 inch water column (W.C.) pressure drop Venturi scrubber. The figure illustrates that both the WESP and Venturi are highly efficient for removing particles greater than 1 micron. The removal efficiency of a Venturi, however, begins to degrade for particles smaller than 1 micron. The Venturi performance can be enhanced by sub-cooling the gas and taking advantage of condensation effects to grow the size of the particulate. The effects of sub-cooling to improve Venturi performance is discussed in greater detail in the Envitech paper, "Wet Scrubbing Technology for controlling biomass gasification emissions" presented at the 2008 Joint Conference: International Thermal Treatment Technologies (IT3) & Hazardous Waste Combustors (HWC).
In general, WESP's are used in applications where the sub-micron particulate concentration exceeds the capability of a Venturi to meet the performance requirements. It is therefore important to understand the following:
A Venturi scrubber will give syngas cleaning performance similar to a WESP. The removal efficiency for particles greater than 1 um diameter will be equal to or greater than a WESP. For particles smaller than 1 um diameter, a Venturi scrubber will be less efficient that a WESP. However, many ICE engines will most likely tolerate these particles. Understanding the tolerance of the engine is therefore a key aspect of deciding which approach is best suited for your application.
Capital Cost - It is broadly understood that a Venturi scrubber is much lower capital cost than a wet electrostatic precipitator. Under most process conditions this cost difference can be as much as 3 to 4 times. The trade-off for a lower capital cost Venturi scrubber is higher operating cost to provide the pressure drop.
The Venturi scrubber capital cost is determined predominately by the size of the gas flow. The WESP capital cost, however, is determined by both the size of the gas flow and the desired removal efficiency. The desired removal efficiency can dramatically affect the size and cost of the system. The higher the removal efficiency, the higher the collection area, and consequently, the greater the number of collection tubes required. The cost of a WESP is approximately exponentially related to the required removal efficiency. It is important to define the performance requirements before budgeting for a WESP.
In addition to metal fabrication, there are other items contributing to the higher capital cost of a WESP, including the T/R set to provide a high voltage, electronics for a more sophisticated control system, and safety interlock system.
Operating Cost - Although a wet electrostatic precipitator is higher capital than a Venturi scrubber, part of that cost is offset by lower operating cost. The pressure drop of a WESP is in the range of a couple of inches W.C. compared to 30 to 50 inches W.C. for a Venturi scrubber. The electricity cost for the fan horse power requirements is therefore considerably lower for a WESP than for a Venturi. There are other WESP operating costs that need to be accounted for including the electricity for the T/R sets and for the heater and blowers for the insulator compartments.
Safety - The last design consideration discussed here for a syngas cleaning system is safety. A key aspect for a syngas cleaning system is that it contains a combustible gas. This carries a greater risk of fire than for other types of scrubber system. If the system is located in a confined space, it is often required for instrumentation and motors to meet division I, class II (explosion proof) requirements. A WESP can operate in sparking mode which can be an ignition source for the gas. Care must be taken to ensure the WESP operates in a safe condition at all times. A WESP has additional safety interlock requirements because it operates at a high voltage. For these reasons, a WESP it is more costly to ensure safety in a WESP than a Venturi scrubber.
Summary
- A Venturi scrubber is lower capital cost than a WESP and in most cases is preferred if it can meet the performance requirements.
- A WESP is generally used in cases where the concentration of sub-micron particulate exceeds the capability of a Venturi scrubber to meet the peformance limits.
- Although a higher capital cost, a WESP has the advantage of lower operating cost. It will also achieve greater overall removal efficiency because it is more efficient for particles smaller than 1 micron.
- Because syngas is a combustible gas, there are safety considerations for both a Venturi scrubber and a WESP. Because a WESP uses a high voltage and can act as an ignition source, the cost to mitigate safety risks is generally considered to be higher than for a WESP.
To learn more, please download our presentation on tar removal.
