As an equipment supplier of custom engineered wet scrubber equipment, Envitech frequently provides lunch and learns (L&L’s) to engineering companies to help educate engineers about the basics of available technology.
Figure 1 below is a summary chart of predominant wet scrubber technology options. The main product categories include packed bed absorbers, Venturi scrubbers, and wet electrostatic precipitators (WESPs). Each wet scrubber type serves a different purpose and is used in different circumstances. For instance, packed bed absorbers are primarily used to remove gaseous emissions like SO2, HCl, or HF. We often receive packed bed absorber inquiries for particulate removal, however, this would be a misuse of technology. Packed bed absorbers remove some particulate but they are not nearly as efficient as other options.
Figure 1: Wet scrubber technology summary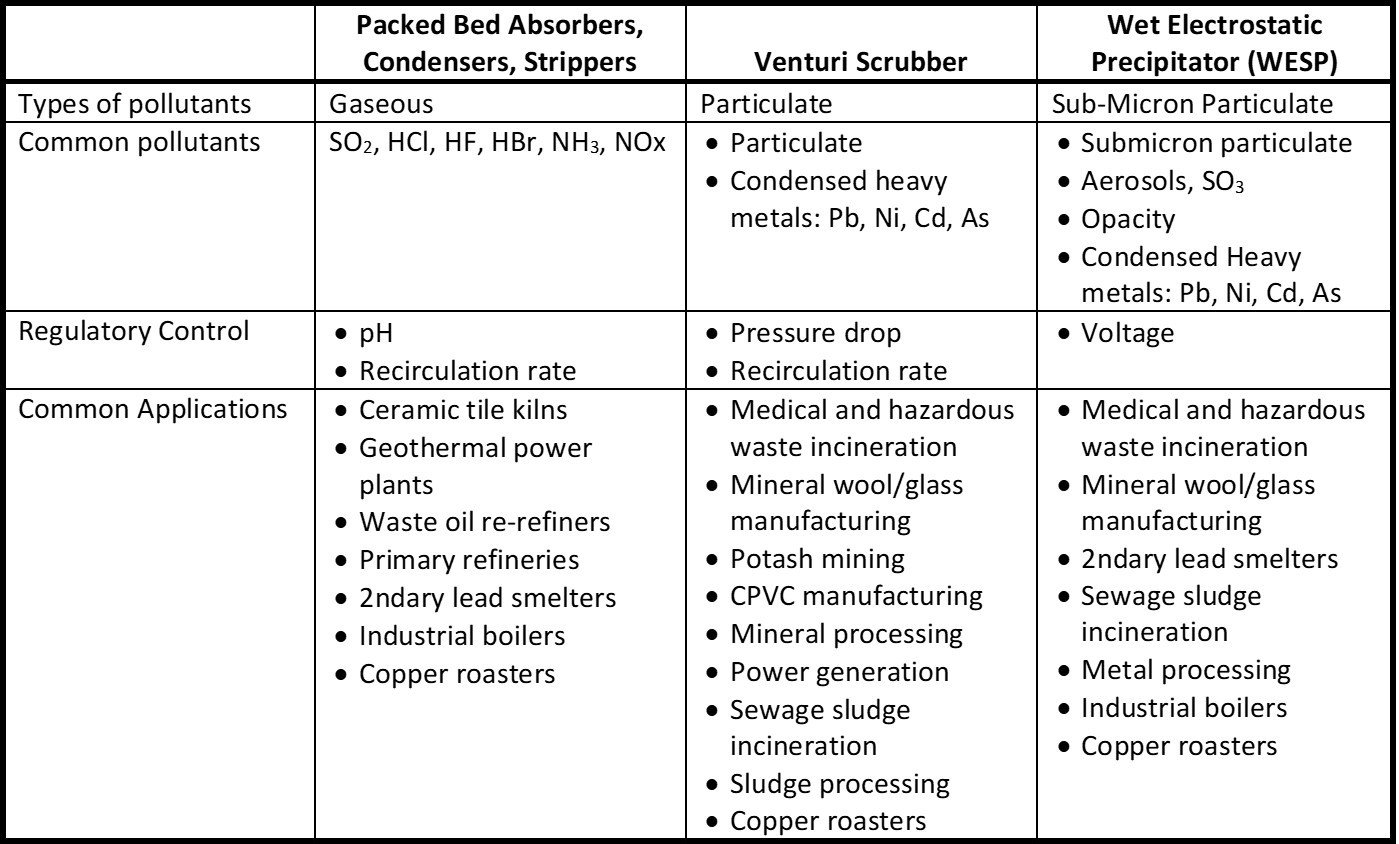
Venturi scrubbers are used for particulate removal. Just like we sometimes receive packed bed absorber inquiries for particulate removal, we’ll occasionally get Venturi scrubber inquiries for acid gas removal. This would also be a misuse of technology. Venturi scrubbers achieve some acid gas removal, but they have poor mass transfer compared to a packed bed absorbers.
Venturi scrubbers use mechanical forces to remove particulate. Particles are captured through a process of impaction between particles in the gas and water droplets in the Venturi throat. A high differential velocity is created between particles and droplets by accelerating the gas in the throat. A pressure drop in the throat provides energy to capture the particles. Smaller particles less than 1 micron in size avoid capture by behaving like gas molecules and finding slip streams around the water droplets. Venturi scrubber performance drops offs exponentially for submicron particulate. Overall removal efficiency may be limited for a gas stream with a high concentration of submicron particulate. Venturi scrubbers are a good choice for industrial dryers or other applications with large size particulate.
Wet electrostatic precipitator (WESP) are the third type of wet scrubber summarized in the table. Like Venturi scrubbers, they are also particulate removal devices. They differ from Venturi scrubbers in a couple of ways, 1.) electrical, not mechanical forces are used to capture particulate, and 2,) they are efficient at capturing submicron particulate. Figure 2 shows a performance comparison between a WESP and Venturi scrubber. It can be seen that performance drops off dramatically for Venturi scrubbers for particles less than 1 micron in size. WESP’s on the other hand remove particles regardless of particle size.
Figure 2: WESP, Venturi scrubber performance comparison versus particle size.
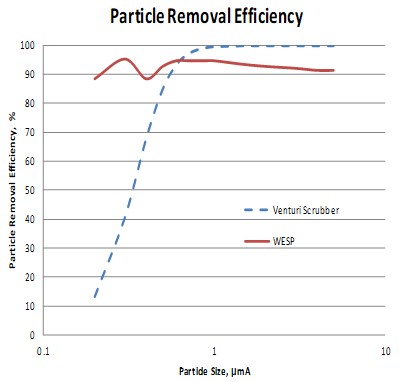
The summary in Figure 1 also shows how each wet scrubber technology differs in regulatory control. A packed bed absorber is typically controlled for recirculation flow rate and liquid pH. A Venturi scrubber is controlled by recirculation rate and pressure drop. A WESP is controlled by voltage. Control limits are typically spelled out in the operating permit.
Finally, some examples of applications are given for each type of wet scrubber. It should be noted that there are many applications that have multiple types of pollutants. A hazardous waste incinerator, for instance, contains particulate, acid gases, and specific heavy metals like cadmium and lead. A fraction of particulate is submicron in size and difficult for a Venturi scrubber to remove. It is common for different types of wet scrubbers to be combined into a multi-pollutant device. Figure 3 shows a common arrangement for an incinerator scrubber. The gas is first cooled in a quencher. A packed bed absorber removes acid gases. A Venturi scrubber removes particulate and a WESP removes the submicron particulate and heavy metals.
Figure 3: Incinerator wet scrubber arrangement
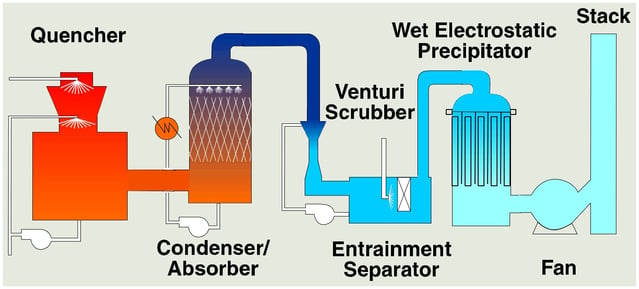
Wet scrubbers can also be combined with dry scrubbers in certain circumstances. An upstream bag-house can remove particulate followed by a packed bed absorber for acid gas removal. A cyclone can be used to knock out large particulate before using a Venturi scrubber for the remaining particulate. A cyclone helps to minimize blowdown and water consumption. In some cases, a dry filter or carbon bed absorber can be integrated downstream of a wet scrubber for mercury and/or dioxin/furan. Click here to read a blog piece about an example of a wet scrubber combined with a carbon bed.
This about covers wet scrubber basics. If you’re with an engineering company and want to discuss scheduling a lunch an learn, please give Envitech a call. You can click on the icon below for a set of Envitech brochures.
Click on the icon below to download an Envitech brochure.
