Venturi scrubbers are mechanical impaction devices that are used to control particulate on a wide range of applications. These include medical and hazardous waste incineration, potash drying, sewage sludge incineration and processing, coal drying, mineral wool manufacturing, and copper roasting to name a few. In one of my last blog posts I discussed a Venturi collision scrubber used to treat exhaust fumes of a Banbury mixer for rubber compounding. The Envitech collision scrubber is used in several Goodyear Tire manufacturing facilities around the world.
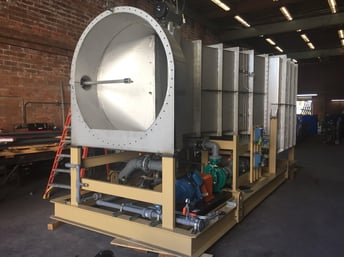
A recent new application is a horizontal Venturi scrubber for an aggregate asphalt drum dyer. The asphalt process is semi-stationary operating at fixed locations for several months at a time. The process is periodically broken down and moved to new locations for operation. The horizontal arrangement makes the horizontal Venturi scrubber an ideal solution for mobile applications. The equipment package is transportable on a single flatbed with only minor disassembly required for shipment and installation. The equipment is mounted onto a skid with pre-assembled piping and wiring to facilitate equipment mobility.
Particles are captured in the horizontal Venturi scrubber through a process of impaction by water droplets injected into the Venturi throat. A fraction of particulate laden water becomes entrained in the gas which has a droplet size distribution. The droplets are removed from the gas by a mist eliminator. There are two pathways for particles to escape capture by the scrubber. The first is penetration. Smaller particles lacking the mass for impaction penetrate through the scrubber. The second is through carry over of particulate laden water droplets. Droplet capture efficiency, or mist elimination, therefore impacts scrubber efficiency and overall plant emissions.
The horizontal Venturi scrubber uses a damper blade and actuator to maintain constant pressure drop across a wide range of gas flows. A high efficiency chevron mist eliminator removes particulate laden droplets before the gas exits the scrubber. A chevron mist eliminator removes greater than 99.9% of water droplets down to 27 microns with less than 0.25 inches W.C. of pressure drop. By comparison, a cyclonic separator requires several inches W.C. of pressure drop to remove 98% of 27 microns droplets. The advantages of a chevron mist eliminator are higher performance, larger turn down ratio, and lower pressure drop.
Envitech is currently building two new horizontal Venturi scrubbers sized for 45,000 acfm each for a peat drying operation. The compact design allows the scrubber to be easily installed inside a building. The high level of pre-assembly and lower profile reduces installation time and improves maintenance access for plant personnel. The horizontal Venturi scrubber can be a cost effective alternative to many processes that use a typical vertical arrangement.
Click on the link below to download Venturi scrubber literature.