There are several industrial processes that face the challenge of meeting increasingly aggressive metals emission standards. In many cases these standards exceed the capability of existing air pollution control equipment which can include bag-houses and packed bed absorbers. Some of these processes include: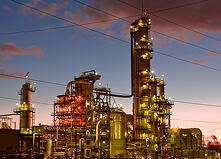
Some of the metals of concern can include mercury, arsenic, lead, cadmium, nickel and others, depending on the process. To achieve more stringent metals emission standards, three features should be designed into the air pollution control system.
Removal of the bulk particulate load - Removal of the bulk particulate load may be required if there is a high particulate concentration from the upstream process. This will be the case for secondary lead smelters, lead refining, and refinery sludge incinerators. Geothermal energy plants will not have this requirement. A bag-house will be used for secondary lead smelters and lead refining. A wet Venturi scrubber system can be used for refinery sludge incinerators Removal of the bulk particulate minimizes space-charge effects inside the WESP. Space-charge effects occur when particles interact and repel each other. This reduces WESP performance because it interferes with the migration of charged particle to the tube wall for collection.
Sub-cooling the gas - Some of the volatile metals may be in the vapor phase when they pass through a bag-house at higher temperature. In this case they will pass right through the bag-house and will not be collected. Sub-cooling the gas is done after the bag-house and uses a condenser/absorber to cool the gas below the saturation temperature. Sub-cooling is beneficial because it condenses as much of the volatile metals as possible so they can later be removed as particulate. In the case where a Venturi is used to remove bulk particulate, like for a refinery sludge incinerator, it has the added benefit of condensing water onto the particulate and condensed metals. This increases their diameter making them easier to remove in a Venturi scrubber. Sub-cooling also reduces the gas volume, which helps to reduce the size and cost of a downstream WESP.
Wet Electrostatic Precipitator (WESP) for polishing - A wet electrostatic precipitator is used as a final particulate polishing stage. The performance is relatively independent of the particle size so it is highly effective at sub-micron particulate control. In some cases, a condenser/absorber (C/A) for sub-cooling can be integrated into the conditioning section of an upflow WESP. This was successfully done at a secondary lead smelter downstream of bag-house. The C/A was also used to neutralize SO2 in the gas stream. The integrated C/A and WESP achieved > 98% removal of arsenic and > 92% removal of lead and other condensed metals after the bag-house. This substantially reduced the plants cancer risk index and helped to meet more stringent fence line lead emission standards.
To download a free white paper on wet electrostatic precipitator for a secondary lead smelter, click the link below.
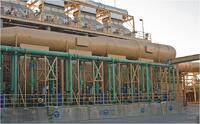
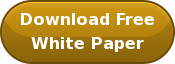
To view a free wet electrostatic precipitator video, click on the link below.
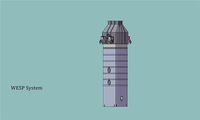
Geothermal by Louis Falcon
Refinery by Szeke